http://www.machinerylubrication.com/Read/29398/unscheduled-oil-analysis
Most oil samples are taken based on a fixed schedule. For large, stationary rotating equipment, monthly or bi-monthly samples are common. Proactive maintenance programs depend on regular checks for oil cleanliness, dryness and lubricant quality. However, machines can and do fail for a variety of reasons, and there is a certain randomness to the onset of these failures. Furthermore, the failure development period is equally unpredictable, with some failures taking months to develop, while others are sudden and abrupt.
In the March-April 2013 issue of Machinery Lubrication, I addressed machine criticality analysis as an essential tool to define the Optimum Reference State (ORS) for numerous lubrication and oil analysis activities. The Overall Criticality Matrix (OCM) is constructed from two assessments: the Machine Criticality Factor (MCF) and the Failure Occurrence Factor (FOF). The MCF relates to the consequences of machine failure while the FOF relates to the probability of machine failure. Both the MCF and the FOF are highly influenced by the effectiveness of “early fault detection.” In other words, the effectiveness of early fault detection sharply reduces machine criticality (for details on this, read the article atwww.machinerylubrication.com/Read/29346/machinery-criticality-analysis).
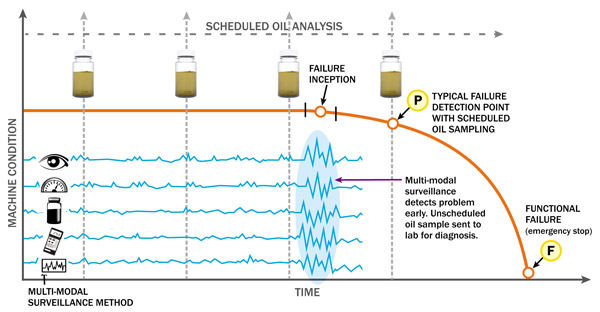
Figure 1. Early Predictive Maintenance P-F Interval Scheme
This is the critical link to the “unscheduled” oil analysis strategy. Its theme is not just predictive maintenance (PdM), but more specifically, early predictive maintenance (EPM). Let’s start by reviewing the widely used P-F interval. A modified version is shown in Figure 1.
The “P” is the point when an abnormal wear condition or fault is first detected. The “F” is the functional or operational end of the failure cycle requiring repair or replacement. Failures with short development periods usually go undetected when tests (e.g., vibration and oil analysis) are performed infrequently (even monthly analysis is viewed as infrequent). Conversely, frequent detection methods not only can report a developing failure but also have the potential to detect that failure early (in the incipient stage). There are specific tactics and tools for doing this well.
Again, the secret to this strategy is the frequency. It enables a much higher percentage of failure detection (saves) events, especially earlier detection. The purposeful benefit is mitigated machine damage and reduced or no unscheduled downtime (longer P-F interval). While PdM concentrates on predicting the end of a machine’s (or lubricant’s) service life, EPM puts critical focus on timing - not just detecting - by detecting early. It seeks a budding problem, not a burgeoning problem.
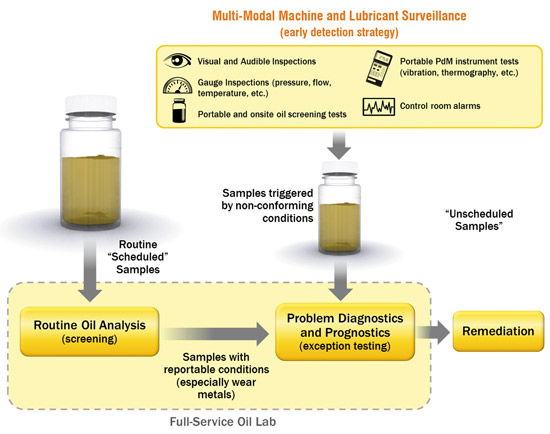
Figure 2. Combining lab data with surveillance data for a complete picture of machine condition
The detection phase of EPM is continuous failure surveillance across numerous parameters. It integrates skillful and frequent human inspection tactics with other conventional monitoring technologies. A few years ago, I wrote a column on the power of the one-minute daily inspection. This is a critical and often underutilized modality of surveillance and detection.
Fundamentally, the detection phase of EPM is anything and everything that can be done to detect (not analyze) failure in progress. It includes all of the following:
Many impending and precipitous failure conditions that were first reported by scheduled oil analysis could have been detected much earlier if better and more frequent inspection methods were in place, such as those in the list above. The economics of early detection are enormously improved as well.
As noted previously, failure detection and failure analysis are different concepts. Once an abnormal condition has been detected, it can be investigated further to determine where it is coming from, the probable cause of the failure, how severe and threatening it is, and the corrective action. This is where oil analysis and other predictive technologies can be very valuable. “Unscheduled” oil samples can then be forwarded to the lab for troubleshooting purposes (diagnostics and prognostics). These include samples from secondary sampling ports to help localize the source of the problem.
In the laboratory, specialized qualitative and quantitative tests can be performed to characterize the nature of the condition. These might include wear particle identification (XRF, SEM-EDX, analytical ferrography and many others). The skills of a triboanalyst and a multi-technology PdM specialist can combine lab data with surveillance data for the most complete picture of the machine’s condition (see Figure 2).
When proactive maintenance is combined with EPM, a comprehensive and more efficient condition-based maintenance program results. Early predictive maintenance is about extreme vigilance. It involves the development of more effective inspection skills and a more effective means of inspection (machine modifications). It also requires a culture change and management support for remediation of machines that have not yet failed.
In the March-April 2013 issue of Machinery Lubrication, I addressed machine criticality analysis as an essential tool to define the Optimum Reference State (ORS) for numerous lubrication and oil analysis activities. The Overall Criticality Matrix (OCM) is constructed from two assessments: the Machine Criticality Factor (MCF) and the Failure Occurrence Factor (FOF). The MCF relates to the consequences of machine failure while the FOF relates to the probability of machine failure. Both the MCF and the FOF are highly influenced by the effectiveness of “early fault detection.” In other words, the effectiveness of early fault detection sharply reduces machine criticality (for details on this, read the article atwww.machinerylubrication.com/Read/29346/machinery-criticality-analysis).
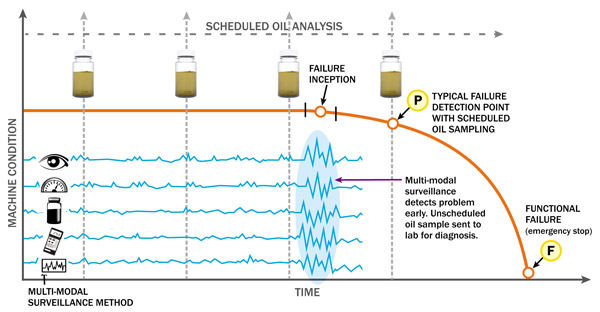
Figure 1. Early Predictive Maintenance P-F Interval Scheme
The “P” is the point when an abnormal wear condition or fault is first detected. The “F” is the functional or operational end of the failure cycle requiring repair or replacement. Failures with short development periods usually go undetected when tests (e.g., vibration and oil analysis) are performed infrequently (even monthly analysis is viewed as infrequent). Conversely, frequent detection methods not only can report a developing failure but also have the potential to detect that failure early (in the incipient stage). There are specific tactics and tools for doing this well.
Again, the secret to this strategy is the frequency. It enables a much higher percentage of failure detection (saves) events, especially earlier detection. The purposeful benefit is mitigated machine damage and reduced or no unscheduled downtime (longer P-F interval). While PdM concentrates on predicting the end of a machine’s (or lubricant’s) service life, EPM puts critical focus on timing - not just detecting - by detecting early. It seeks a budding problem, not a burgeoning problem.
Detection by Multi-Modal Surveillance
In Noria’s seminars, we use the expression, “You can’t catch a fish unless your hook is in the water.” Likewise, in oil analysis, you can’t catch a fault unless your hook is in the water. There’s an earlier tier to oil analysis called the “detection phase,” which in my view is a huge untapped opportunity in condition-based maintenance. Most scheduled oil analysis programs skip over the detection phase by attempting to catch impending machine failures and only take infrequent snapshots of oil condition.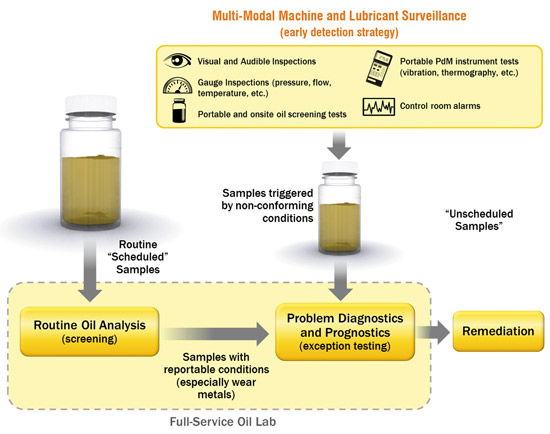
Figure 2. Combining lab data with surveillance data for a complete picture of machine condition
Fundamentally, the detection phase of EPM is anything and everything that can be done to detect (not analyze) failure in progress. It includes all of the following:
- Daily routine visual inspections of the oil (level, color, opacity, foam, varnish, tank condition, leakage, magnetic plugs, etc.)
- Audible inspections (change in machine sound)
- Temperature inspections (touch, heat guns, gauges, etc.)
- Portable PdM technology inspections (vibration overalls, thermography, acoustics, motor current, etc.)
- Mechanical inspections (shaft movement, seal conditions, open gear wear, etc.)
- Instrument and gauge inspections (flow rates, proximity probes, pressure, bypass indicators, etc.)
- Onsite oil analysis screening tests (crackle, blotter, viscosity, ferrous density, patch, etc.)
Many impending and precipitous failure conditions that were first reported by scheduled oil analysis could have been detected much earlier if better and more frequent inspection methods were in place, such as those in the list above. The economics of early detection are enormously improved as well.
As noted previously, failure detection and failure analysis are different concepts. Once an abnormal condition has been detected, it can be investigated further to determine where it is coming from, the probable cause of the failure, how severe and threatening it is, and the corrective action. This is where oil analysis and other predictive technologies can be very valuable. “Unscheduled” oil samples can then be forwarded to the lab for troubleshooting purposes (diagnostics and prognostics). These include samples from secondary sampling ports to help localize the source of the problem.
In the laboratory, specialized qualitative and quantitative tests can be performed to characterize the nature of the condition. These might include wear particle identification (XRF, SEM-EDX, analytical ferrography and many others). The skills of a triboanalyst and a multi-technology PdM specialist can combine lab data with surveillance data for the most complete picture of the machine’s condition (see Figure 2).
Proactive Maintenance Still Requires Scheduled Oil Analysis
Unscheduled oil analysis is not an alternative to scheduled oil sampling and analysis. Routine oil analysis is still needed for many reasons. The most important is proactive maintenance, which uses oil analysis to monitor and control the presence of failure root causes. These include verification of the lubricant’s physical and chemical properties as well as contamination control. The benefits of a fine-tuned proactive maintenance program are much slower machine wear rates (longer machine service life), fewer overall machine failures and less associated downtime.When proactive maintenance is combined with EPM, a comprehensive and more efficient condition-based maintenance program results. Early predictive maintenance is about extreme vigilance. It involves the development of more effective inspection skills and a more effective means of inspection (machine modifications). It also requires a culture change and management support for remediation of machines that have not yet failed.
About the Author
No comments:
Post a Comment